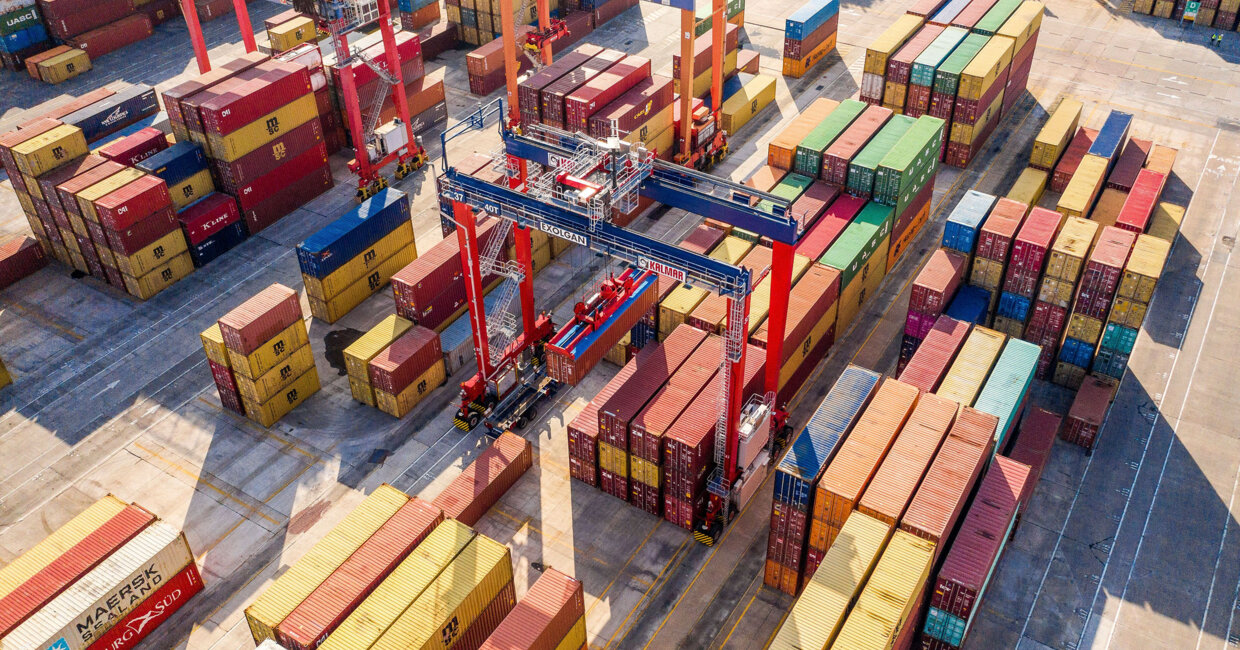
Smart design and driveline choices help in enhancing RTG eco-efficiency
As the drive to improve environmental performance at container terminals continues to gather pace, operators are faced with several choices when it comes to expanding or renewing their rubber-tyred gantry (RTG) crane fleets in order to achieve sustainability gains. With smart choices on both the crane base design and energy systems, the crane's eco-efficiency can be improved considerably.
Before we start thinking about which RTG driveline is the optimal choice in terms of eco-efficient operations, there are several other design details that can help to achieve big gains in fuel efficiency.
“We have worked for decades to improve the eco-efficiency of cargo handling, and our RTG offering is a great example of this,” says Marko Rasinen, Product Manager, RTG, Kalmar Automation Solutions.
Lighter, simpler and easier to maintain
Structural design, essentially the weight of the crane, makes a big difference when it comes to fuel consumption. By simplifying the design and optimizing the structure with high-grade steel it’s possible to save up to 0.5 litres of fuel per hour. Lowering the weight of the crane has some positive knock-on effects too, like reduced ground pressure, which reduces civil works costs.
The choice of all-electric vs. hydraulic design is another important consideration. Hydraulic setups have traditionally been used for spreaders and for gantry-wheel turning and micromovements, but switching to all-electric can cut fuel consumption by as much as two litres per hour, with the added bonus of reduced maintenance costs because of fewer moving parts. Additionally, there will be no oil leaks in case the actuator breaks.
“The combined weight of the spreader/head block unit makes a big difference too since this equipment is lifted and lowered twice every move. Minimising the weight here can deliver up to a litre of fuel savings per hour,” Marko points out. “Even lighting can make a contribution, with energy-efficient LED lights offering a potential saving of 0.5 litres of fuel per hour,” he continues.
Finally, there’s the choice of variable speed generator (VSG) vs. constant speed generator. By matching engine RPMs with the necessary power, a VSG can achieve potential fuel savings of as much as 2.5 litres per hour.
One size doesn't fit all
What’s right for one terminal might not be right for another, no matter how similar their operational setups. Having a range of alternatives is therefore important. In terms of drivelines, with the Kalmar RTG, there are plenty to choose from: the fully electric Kalmar Zero Emission RTG, the diesel-powered Kalmar SmartPower RTG and Kalmar Classic RTG, and the Kalmar Hybrid RTG, which uses lithium-ion (Li-ion) battery packs as its main source of energy.
This last variant has been a popular choice with terminal operators of all kinds around the world because of its huge potential for fuel and emission savings.
“The Li-ion batteries, which come with a five-year warranty, are combined with a smaller diesel power unit, which is not only highly fuel-efficient – consuming as much as 60% less fuel (typically around 6.5 litres per hour) than a conventionally powered RTG, with a corresponding reduction in CO2 emissions – but also quieter and easier to maintain,” Marko explains.
The diesel power unit’s running hours are significantly reduced because it is not used to power any of the crane functions, only to charge the batteries – which take care of all the lifting, lowering and driving operations. Fewer engine running hours not only means less fuel is consumed but also less component wear. And with the batteries doing all the work, noise emissions are also significantly reduced. “The batteries are also virtually maintenance-free, requiring only checkups,” Marko highlights. “Furthermore, they can store regenerative energy from lifting and lowering operations, which is an important factor in achieving such low fuel-consumption levels.”
An attractive option where full electrification isn’t possible
While going fully electric is the preferable option from a sustainability perspective, in some locations it simply isn’t viable. Hybrid technologies are a particularly attractive alternative to fully electric drivelines in markets where the quality and reliability of the electricity supply may be poor, or at terminals where the existing infrastructure may not support a cable-reel or bus bar setup.
Hybrid RTG drivelines have developed significantly in recent years, offering even greater gains in fuel efficiency and reductions in emissions and noise. Kalmar’s second-generation hybrid RTG is a highly fuel-efficient machine that makes no compromises on performance.
The new Kalmar Hybrid RTG builds on the proven, sustainable performance of the previous-generation model to deliver even greater savings in fuel efficiency, airborne and noise emissions, and maintenance costs.
The super-capacitor system of the previous model has been replaced by the latest lithium-ion (Li-ion) battery technology, which has a much higher energy-storage capacity. However, just like the previous-generation model, the new Kalmar Hybrid RTG features a regenerative energy system that stores energy generated by braking and spreader-lowering for later use.
The gains in terms of fuel efficiency and lower maintenance requirements can be explained in extremely simple terms: the power unit’s running hours are significantly reduced because it is not used to power any of the crane functions, only to charge the Li-ion battery. Fewer engine running hours means less fuel consumed and less component wear. And with the battery doing all the work – powering the lifting and driving operations – noise emissions are also significantly reduced.
Over the years, our industry has made tremendous strides in developing the eco-efficiency of cargo and material handling through more efficient machines, optimisation of cargo flows, as well as intelligent equipment and automation. With its ability to cut the cost of every container move while also minimising environmental impact, hybrid RTG technology is a highly attractive option for many terminals around the world. Smart design thinking and the right choice of driveline helps terminals improve their eco-efficiency by delivering impressive savings for operations in terms of fuel, emissions, maintenance and noise levels.
Marko Rasinen
Product Manager, Kalmar Automation Solutions
Marko has over 20 years of experience in product management, sales and engineering of Yard Cranes. Marko’s vast experience in the customer interface as well as with Kalmar engineering teams has helped him form a comprehensive understanding of the customers’ business environment as well as the technological capabilities that modern technology offers. Today Marko manages the Rubber Tyred Gantry Crane offering at Kalmar, working together with the customers, suppliers and internal engineering teams securing the development of high-quality products matching the customer needs.
Related articles
Subscribe and receive updates in your email
Prenumerera på våra publikationer