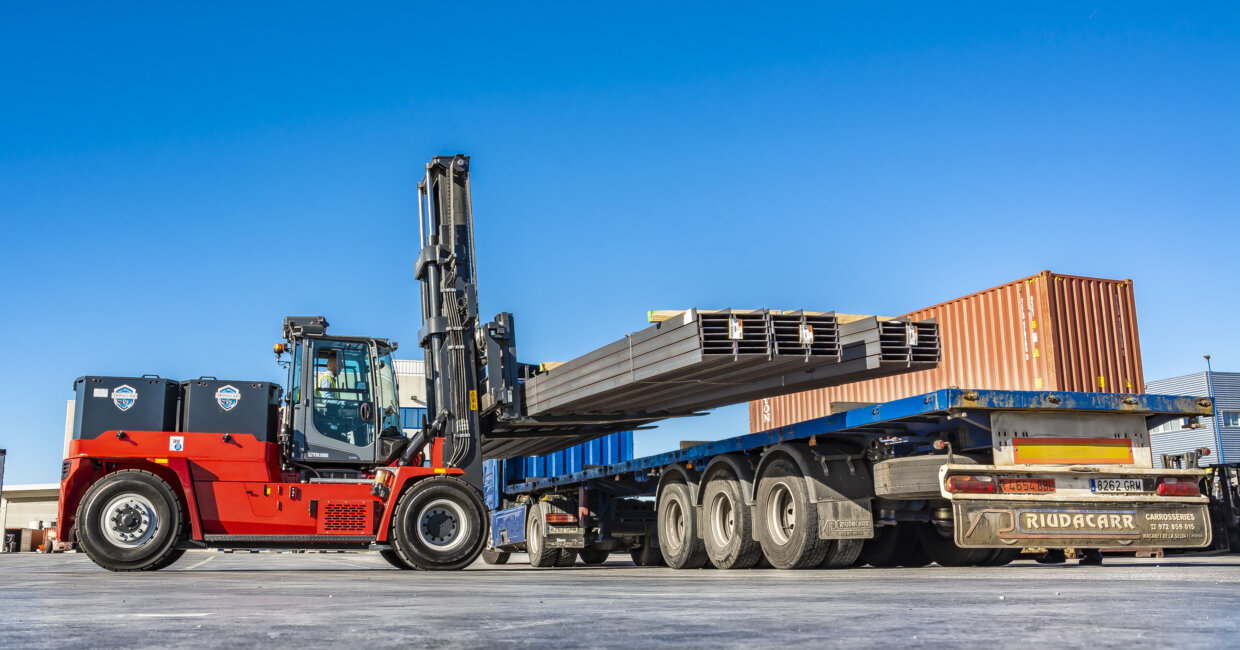
Driving internal logistics electrification
There are many ways in which customers can benefit from internal logistics electrification. From operator safety to environmental performance, electric forklifts not only perform well - they also enable users to meet a range of key business objectives.
Kalmar has been in the vanguard of electric powered vehicle development over the last 30 years. In 2018, the company evaluated and tested fuel cell technology for forklifts in collaboration with SSAB and has committed to electrifying its entire machine range by 2021.
The first reason for going electric is safety, explains David Malmström, Business Development Manager, Kalmar Forklifts. “Electrical machines not only eliminate carbon emissions, they also reduce vibrations and lower operational sound levels significantly, creating a more pleasant environment for the driver and their colleagues working in the same area.”
A diesel forklift operating for 2,200 hours annually will produce 37 pounds of carbon dioxide - compared to an electric truck that only produces four pounds.
Great environmental impact
Then there is the environmental impact. A diesel forklift operating for 2,200 hours annually will produce 37 pounds of carbon dioxide - compared to an electric truck that only produces four pounds – and has more predictable operating costs because electricity is less vulnerable to price fluctuation than diesel. Electric powered machines also require less maintenance and servicing.
Companies embarking on electrification should start by mapping their drive cycles to determine where and how their forklifts are driven. This is important because infrastructure needs to be adapted to optimise processes.
“For example, the charger for the machine should be strategically positioned and the charging cycling optimised for maximum availability,” explains Malmström. “The battery will work at its best if it is integrated with driving cycles. It is also important to understand whether the existing power supply is sufficient and whether ventilation requirements have been met – just some of the issues on which we can advise customers.”
Kalmar’s work on battery technology for mobile solutions enables it to offer two options depending on how the machine is to be used. Lead acid batteries are optimised for working non-stop in one shift and being recharged, whereas operations that allow for ‘opportunity charging’ (during driver breaks, for example) may be better suited to lithium ion batteries.
The process of changing the battery can be completed in around five minutes and charging takes approximately eight hours for lead acid and 1,5 hours for Li-ion for a full charge.
“Our electric forklift matches the diesel equivalent in all aspects but it also has a faster acceleration as full power is available instantly and runs more smoothly."
Full power is available instantly
Performance is obviously a major consideration. “Our electric forklift matches the diesel equivalent in all aspects but it also has a faster acceleration as full power is available instantly and runs more smoothly,” says Malmström.
Kalmar Insight enables customers to monitor energy consumption, driving cycles and machine status as well as schedule maintenance.
“The major difference between diesel and electric trucks is the number of moving parts in the driveline, which is significantly lower on the electric machine due to the absence of a combustion engine, cooler, turbo or starter engine,” explains Malmström.
“Since there are also fewer liquids and filters to maintain, this means that although service intervals are the same as with the diesel forklift, maintenance is much less expensive and requires less downtime, which is a further cost saving.”
Kalmar analysis of a 16 ton diesel-driven forklift and the electric-driven equivalent driven under the same conditions over a five year period has found that while the purchase price of the electric vehicle is higher due to the cost of the battery and charger, total cost of ownership over the five years could in a European country be 28% less than for the diesel machine.
Customers have a number of purchasing options for embarking on their electrification process. These include:
- Direct purchase, where the customer buys and owns the machine and servicing is provided either in-house or by Kalmar
- Leasing, where the customer pays a monthly fee and servicing is provided in-house or by Kalmar
- Rental, where the customer pays a monthly fee for the machine and servicing is provided by Kalmar
“We also offer customised solutions,” concludes Malmström. “This underlines the simplicity of transitioning to electric powered forklifts. Of course customers need to plan for the change, but once they get started they realise that this is just another way of powering their machines – and one that is appreciated by operators and customers alike.”
David Malmström discussed issues relating to internal logistics electrification during a webinar hosted by Kalmar in June – a recording of the webinar is available at https://www.kalmarglobal.com/news--insights/webinars/an-electric-driven-forest-industry/
Related articles
Subscribe and receive updates in your email
Prenumerera på våra publikationer