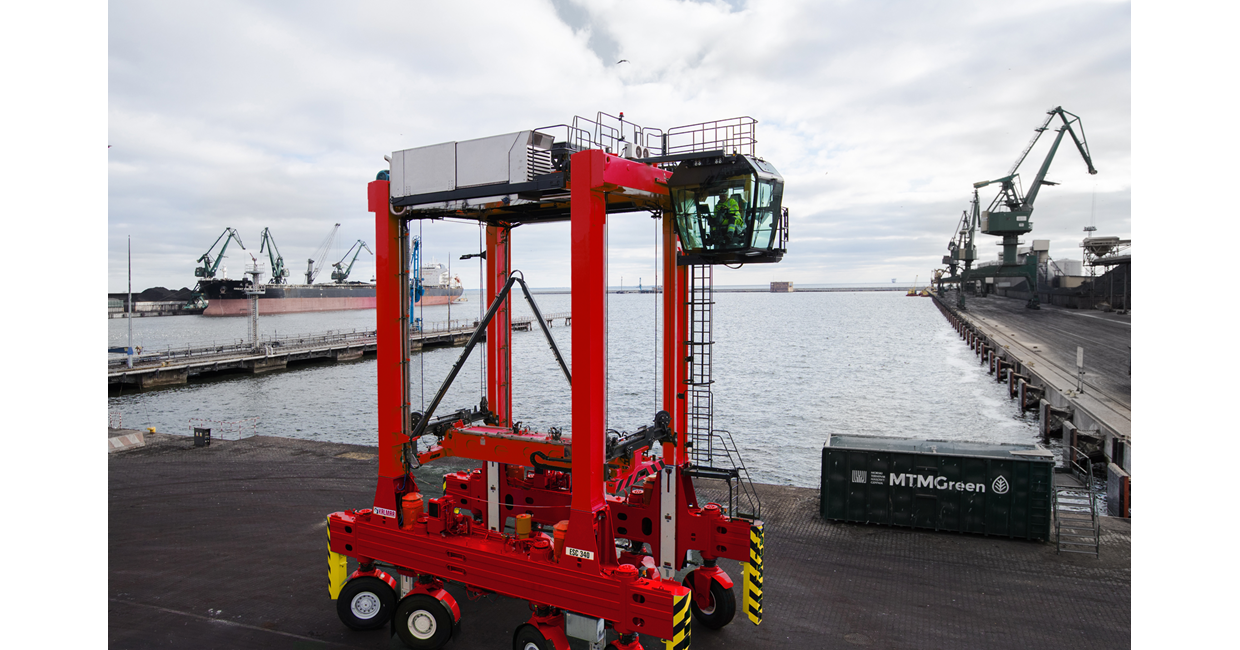
The best of both worlds for straddle and shuttle carrier operations
The backbone of container terminals the world over for decades, straddle and shuttle carriers have undergone many technological transformations in their time – not least in terms of their drivelines.
Powered by the latest in lithium-ion (Li-ion) battery technology, today’s hybrid models can offer potential benefits in terms of reductions in fuel consumption as well as noise and exhaust emissions, but quantifying these has to be rooted in hard facts instead of mere guesswork. With support from Kalmar, terminal operators can clearly identify the potential savings and benefit from the best of both worlds – the performance of a diesel machine enhanced with the environmental advantages of the latest hybrid technologies.
Kalmar’s expertise in straddle and shuttle carriers goes back a long way. Our first toplift-type straddle carrier started its working life with a customer in North America 50 years ago. Since then, 5,500 more machines have rolled off the production line ready for delivery to container terminals around the world. With container terminals under increasing pressure to improve their environmental performance while simultaneously increasing operational efficiency, many operators have turned to hybrid technologies to help them achieve gains in fuel efficiency and reductions in emissions, noise and maintenance costs.
Delivering the goods since 2013
The story of Kalmar’s hybrid straddle and shuttle offering began almost a decade ago, way back in 2010, when we made a strategic decision to start developing eco-efficient versions of our products. The first hybrid machines were launched just three years later in 2013, and in the intervening five years our eco-efficient offering has grown to encompass a wide range of leading-edge environmentally friendly technologies that support our customers with their business goals.
Li-ion battery technology has developed rapidly, and today powers everything from phones and personal computers to electric cars and buses. There has been steady progression in both performance and capacity, and according to our own measurements the technology now offers a level of stability and consistency in terms of energy storage that solutions based on supercapacitors cannot offer in hybrid horizontal transport operations.
Savings all round
In Kalmar hybrid straddle and shuttle carriers the Li-ion batteries are combined with a compact diesel power unit, which is not only highly fuel-efficient, but also quieter and easier to maintain than the unit in a machine powered by diesel alone. They also come with a maintenance-free regenerative energy system that converts energy from deceleration and spreader lowering into electrical power, which is then stored in the battery system.
The gains in terms of fuel efficiency and lower maintenance requirements can be explained in pretty simple terms: the fit-for-purpose diesel unit works as a primary energy source and runs in an optimised way to provide the power required to operate the machine. An energy storage unit linked to the system is used to stabilise usage of the energy. This translates into less engine hours, which in turn reduces both fuel consumption and component wear.
The proof is in the numbers. Since the technology was first introduced in 2013 Kalmar has sold close to 200 hybrid machines to various terminal customers around the world. In terms of cost savings, Kalmar hybrid straddle carriers have enabled on average a 30% reduction in fuel consumption compared to diesel-powered machines.
What’s more, with the battery powering the lifting and driving operations, noise emissions can be reduced by approximately two decibels. With hybrid technologies it’s easy to get fixated on fuel savings and emission reductions alone, but noise reduction is becoming an increasingly important consideration for many container terminals, especially those located close to populated areas.
In terms of driver behaviour, hybrid machines also offer the opportunity to change the way in which machines are used in order to gain maximum benefit. With fully electric operations on the radar of many terminal operators around the world, hybrid straddle and shuttle carriers can act as a “stepping stone” towards solutions such as Kalmar FastCharge™ machines.
Since the technology was first introduced in 2013 Kalmar has sold close to 200 hybrid machines to various terminal customers around the world.
Benefit calculations based on facts, not guesswork
When terminal operators are considering the switch to hybrid machines, our approach at Kalmar is rooted in demonstrating the realistic benefits using hard facts and figures. It’s important to remember that every terminal is different, and you can’t apply a cookie-cutter approach when making claims about the potential savings and other benefits of hybrid machines.
Instead of loose promises based on assumptions or general models, we work closely with customers to analyse their operations and collect data to help us demonstrate the potential fuel savings and other benefits of switching to hybrid. It’s an non-invasive, hassle-free and completely secure process for the customer. We simply collect some specific operational data from the diesel machine’s control unit, and based on this we can provide a clear and realistic representation of the benefits that can be expected by switching from a diesel to a hybrid machine. Further down the line, should an operator look to electrically powered solutions like Kalmar FastCharge our team can also recommend the optimal number and locations of charging stations for the machines.
With support from Kalmar, terminal operators can clearly identify the potential savings and then benefit from the best of both worlds – the performance of a diesel machine enhanced with the environmental and cost-related advantages of a modern hybrid driveline.
Related articles
Further reading
Subscribe and receive updates in your email
Prenumerera på våra publikationer