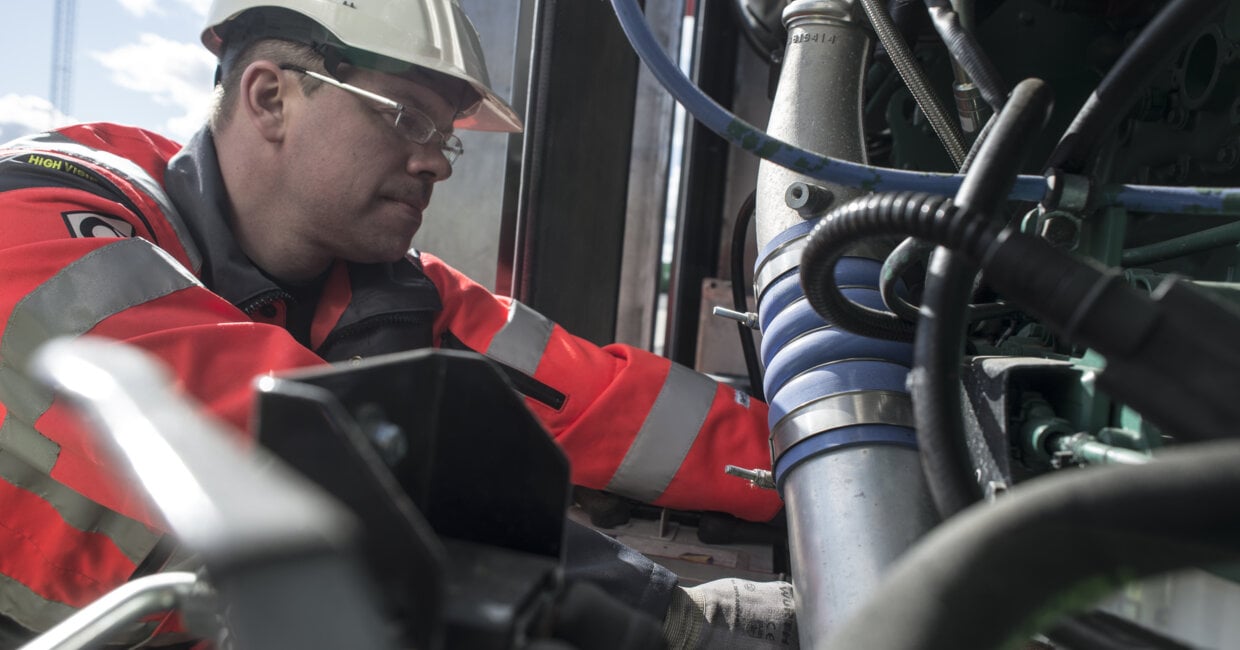
Service collaboration - ten years and still counting
Suomen Satamatekniikka, a subsidiary of Finland’s biggest stevedoring services provider Steveco, owns and operates the cargo handling machinery used by the Steveco Group. One of Satamatekniikka’s major operating sites is the Vuosaari port terminal in Helsinki. The company has handled cargo at the terminal since 2008, and has been a steady Kalmar Service client throughout the 10 years.
Satamatekniikka’s parent company Steveco has relied on what is now Kalmar since the 1970s. The company purchased its first Kalmar carriers in 1994–95 and has continued using Kalmar equipment throughout the decades, relying on Kalmar’s maintenance services all during this time. Satamatekniikka has operated at Vuosaari ever since the port opened in 2008.
A broad coverage contract
Starting from a clean slate, Satamatekniikka wanted to outsource their equipment maintenance instead of having their own repair shop. The new model aimed at improved efficiency combined with savings in resources.
“We wanted to ensure that we have a reliable and competent provider who secures uninterrupted operation for Steveco’s equipment,” says Matti Harju, Manager, Machinery Unit, Suomen Satamatekniikka.
The contract, a slightly customised Kalmar Complete Care, covers 16 of the operator’s current fleet of 20 straddle carriers at Vuosaari, with an option for two additional ones from May 2018. It is a tribute to the quality of Kalmar’s service that Satamatekniikka is now into its fourth consecutive contract period – ten years of unbroken satisfaction.
A day in the life of Kalmar Service
A typical weekday for the morning shift of Kalmar’s nine service technicians starts at six in the morning. The evening shift takes over at two in the afternoon and works until 10pm, corresponding to Satamatekniikka’s working rhythm.
The carriers are taken for regular servicing every 1,000 work hours, which creates a hefty amount of work as the newest carriers drive some 4,500 hours yearly. When problems arise outside regular servicing and maintenance, these repairs need to be figured into the work schedule.
Prepared for all contingencies
Besides performing scheduled service, the personnel is always prepared for more hectic assignments. "The equipment must run without disruptions,o glitches demand immediate action, sometimes within only minutes," says Perttu Kojonen, Senior Service Manager, Kalmar. “In acute situations, you jump into action immediately. We need to be very good at prioritising.”
Speed is also of the essence when a scheduled service takes longer than expected. That increases the workload for the rest of the fleet, which makes it all the more important to be on standby for any contingencies.
“It tends to be that successes and wins are a given, but the unexpected surprises are the hallmark of Kalmar’s service hallmark of competency and efficiency when we run into really big problems,” says Harju.
Kojonen is especially proud of the skill and competence of his personnel. “We are able to keep the customer’s fleet running while handling unexpected situations without disruptions to their operations while at the same time staying on schedule with periodic services.”
“We are able to keep the customer’s fleet running while handling unexpected situations without disruptions to their operations."
Efficient work processes
Because Satamatekniikka operates Kalmar equipment, Harju says it was only natural to opt for the manufacturer's maintenance services to make sure the equipment is always serviced and repaired according to the manufacturer's guidelines.
Every machine’s service history is carefully recorded and analysed, and projections of future needs is made based on that data. For new machinery for which there is no history, the service unit uses the expertise of the central organisation’s procurement specialists.
In winter, planning and operational demands increase significantly. The equipment is exposed to far greater structural loads because of snow, and deep sub-zero temperatures that pose their own challenges.
“When the day is sunny and reasonably warm, but during the night the temperature drops to minus twenty-five degrees celsius, it takes real expertise to bring the deep-frozen machines back to life in the morning,” Kojonen says.
It is with barely concealed pride that he mentions how his team is able to keep its commitments to its customers even in the harshest conditions.
Outstanding technology boosts maintenance
According to Kojonen, Kalmar equipment’s linear construction and high quality components play a significant role in maintenance, but so does the fact that the service organisation is the manufacturer’s own.
“We have access to everything down to the original drawings, and our planning and troubleshooting software sets us apart from most other organisations,” says Kojonen. “We know the equipment inside out. For engines and powertrains, I think there is no one else who has as advanced tools as we have.”
Harju of Suomen Satamatekniikka agrees. “Kalmar equipment was a natural choice since we know Kalmar's machines well, spare parts availability has proven to be excellent, and we have a long history together.”
The future - technological change and solid service
World trends are pointing to an electrical future. Mechanical engineering will make room for electrical engineering with entirely new competency requirements for service.
“Electrical work requires a certification, which is a big change from today,” Kojonen explains. “Then again, many aspects of maintenance will become more sustainable and require less work. For example, we don’t need to fix so many mechanical parts, and when we get rid of 95 percent of used oils, it is a significant environmental and workload factor.”
Kalmar believes that new container handling equipment will be electrically powered in ten years’ time. Kalmar Service, also at Vuosaari, is prepared for the future for the benefit of its clients.
Both men have a very positive view of their companies’ future together. “We definitely wish to continue and develop our collaboration with Kalmar Service,” says Harju.
Related articles
Further reading
Subscribe and receive updates in your email
Prenumerera på våra publikationer